포스코 광양제철소 풀필먼트센터 가보니
제조업 최초 자재 보관 풀필먼트 구축
포스코DX 협업해 안전성·생산성 높여
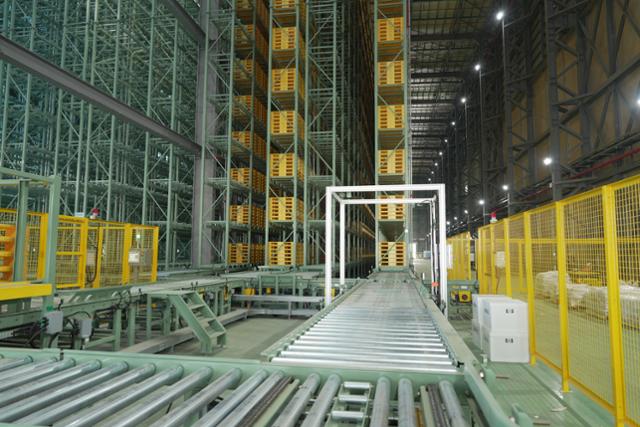
14일 전남 광양시 포스코 광양제철소 풀필먼트센터에서 체적 측정을 마친 자재들이 자동화 창고에 저장된 모습. 포스코DX 제공
제철소에 필요한 자재가 있으면 현장 작업자들이 풀필먼트(통합물류) 센터까지 안 와도 됩니다. 모바일이나 태블릿 앱으로 자재 이미지와 위치를 확인해 주문해요
임호성 포스코DX PM
14일 전남 광양시 포스코 풀필먼트센터. 축구장 7개 크기인 연 면적 5만 제곱미터(㎡) 규모의 드넓은 곳에서 만난 임호성 포스코DX 광양압연자동화그룹 프로덕트 매니저(PM)는 태블릿PC를 가리키며 이렇게 말했다. 4월 포스코와 포스코DX가 협력해 준공한 제조업 최초의 통합물류 시스템 완성도에 대한 자신감이 느껴졌다.
풀필먼트센터는 정보기술(IT), 자동화기술(OT), 인공지능(AI), 로봇 등의 기술을 이용해 구축한 물류 입고-보관-재고관리-포장-검수-배송 등을 통합 서비스하는 곳을 뜻한다. 물류 기업들이 신속하고 정확한 배송을 위해 고안한 개념인데 포스코가 제조업 현장에 처음 도입했다. 제철소 자재를 300여 개 창고에 나눠 보관했던 비효율을 개선하기 위해서다.
제철소 현장 맞춤 설계… 웨어러블 스캐너로 자재 무게 측정
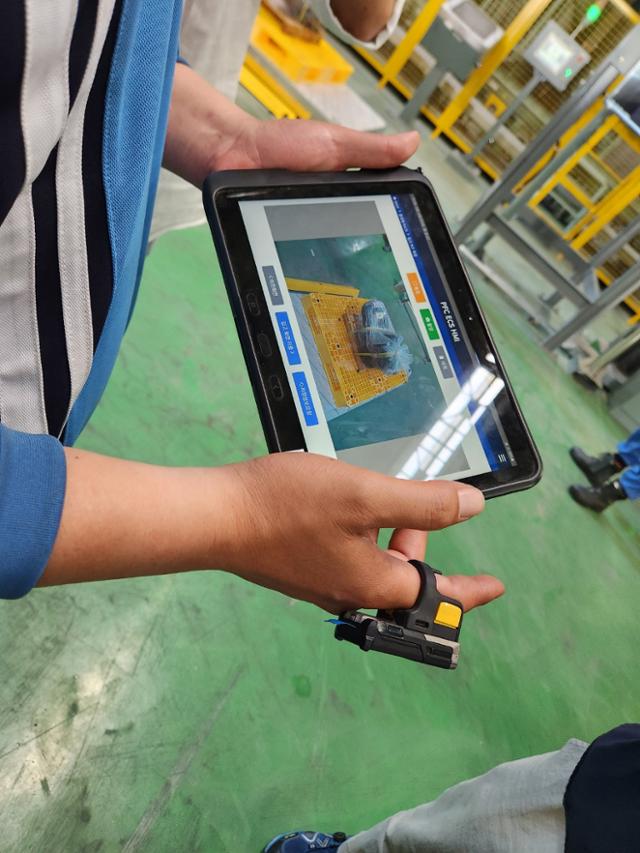
14일 전남 포스코 광양제철소 풀필먼트센터에서 작업자가 손가락에 착용한 웨어러블 스캐너로 부품 무게를 측정한 뒤 태블릿PC를 통해 자재 위치를 파악하고 있다. 광양=김지현 기자
이 센터는 물류기업과 다르게 속도보다 제조업 현장 작업자들의 편의와 안전을 최우선으로 고려한 곳이다. 제철소는 고위험·고강도 현장이어서 자재를 제때 공급하는 게 첫 임무이다. 임 PM은 "신입사원이 오거나 담당자가 바뀌더라도 자재의 종류와 수량을 쉽게 파악할 수 있게 사진으로 분류했다"고 설명했다.
제철소 조업에 필요한 다양한 규격의 자재를 저장할 수 있게 맞춤 설계된 점도 눈에 띄었다. 포스코 풀필먼트센터는 최대 1톤(t)에 달하는 대형 자재부터 안전모나 안전화까지 보관해야 한다. 그래서 자재 크기별로 나뉜 3만4,000개 이상의 셀(Cell·선반)이 있다. 3D 스캐너가 대·중·소로 크기를 분류한 뒤 작업 활용도를 고려해 저장할 선반을 정하면 로봇인 스태커 크레인(Stacker Crane)이 움직이며 중대형 자재들을 보관·출고하도록 시스템이 짜여 있다.
활용법은 간단했다. 이날 웨어러블 스캐너를 착용하고 태블릿을 든 작업자가 풀필먼트센터에 입고된 자재를 팔레트에 올리자 자동으로 크기와 무게가 측정됐다. 작업자는 태블릿PC 내 버튼만 누르면 스태커 크레인이 내려와 부품을 알아서 옮겼다. 작업자들은 자재의 위치와 상태도 실시간으로 창고 관리 시스템(WMS)을 통해 확인할 수 있었다. 데이터를 가지고 자재 수요 예측과 재고 관리가 가능하단 뜻이다.
현재 12인이 센터를 관리하고 있다. 임 PM은 "물건을 옮기고 저장하는 작업은 거의 로봇이 맡고 사람은 자재를 분류하거나 행정 업무를 한다"고 설명했다.
고위험 현장엔 로봇 투입… "생산성보다 안전성이 우선"
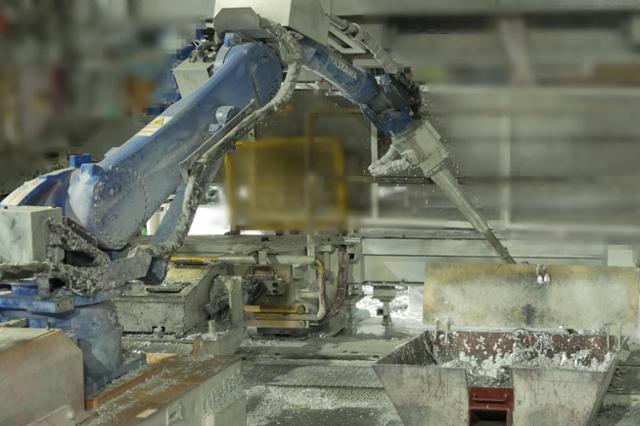
전남 포스코 광양제철소 도금공장에 적용된 드로스 제거 로봇. 포스코DX 제공
포스코는 고위험 현장의 로봇 도입에도 속도를 내고 있었다. 광양제철소 4도금 공장에 가보니 높이 2m의 로봇이 카메라에 달린 비전 AI로 이물질을 확인한 후 뜰채가 달린 팔로 제거했다. 과거에는 460도에 달하는 포트 옆에서 작업자 네 명이 한 조가 되어 하루 10회씩 이물질을 긁어내야 했는데 이를 로봇에 맡긴 것. 가공된 철판을 코일로 감고 밴드커터로 끊는 고강도 작업도 로봇의 몫이다.
이 공장을 둘러보니 사무실이나 관제소 외에 작업자들은 많이 보이지 않았다. 도금을 마치고 품질 검사를 끝낸 철판의 라벨링 작업도 로봇이 할 만큼 자동화가 상당 부분 진행돼 있다. 현장을 안내한 윤석준 포스코DX 로봇자동화센터장(상무)은 "광양제철소의 자동화 수준은 세계적으로도 상당히 높고 현재도 산업용 로봇 현장의 특성에 맞게 시스템을 설계하고 구축해가는 과정"이라며 "그래도 1순위 고려 사항은 안전"이라고 강조했다.
기사 URL이 복사되었습니다.
댓글0